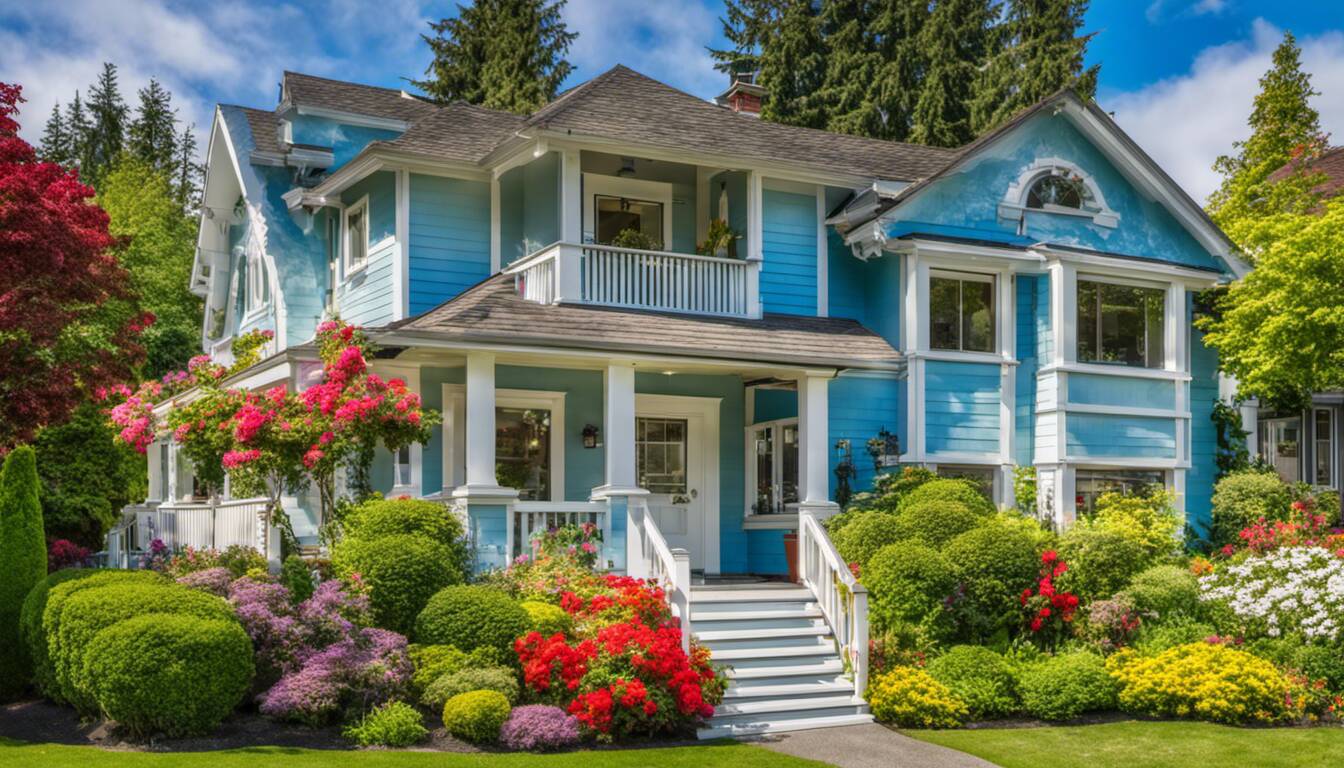
');--success-svg-icon:url('data:image/svg+xml;utf8,');--info-svg-icon:url('data:image/svg+xml;utf8,');--chevron-svg-icon:url('data:image/svg+xml;utf8,');--checkbox-svg-icon:url('data:image/svg+xml;utf8,');--radiobutton-svg-icon:url('data:image/svg+xml;utf8,');--show-password-svg-icon:url('data:image/svg+xml;utf8,');--hide-password-svg-icon:url('data:image/svg+xml;utf8,');--error-svg-icon-color:var(--red-500);--success-svg-icon-color:var(--emerald-700);--info-svg-icon-color:var(--sky-500);--chevron-svg-icon-color:var(--grey-900);--checkbox-svg-icon-color:var(--grey-900);--radiobutton-svg-icon-color:var(--grey-900);--show-password-svg-icon-color:var(--grey-900);--hide-password-svg-icon-color:var(--grey-900);--bde-woo-notices__icon-size:16px;--bde-woo-notices__padding:24px;--bde-woo-notices__border-radius:4px;--bde-woo-notices__error-background:var(--red-50);--bde-woo-notices__error-text:var(--red-500);--bde-woo-notices__error-link-text:var(--red-500);--bde-woo-notices__error-link-text-hover:var(--red-500);--bde-woo-notices__info-background:var(--sky-100);--bde-woo-notices__info-text:var(--sky-500);--bde-woo-notices__info-link-text:var(--sky-500);--bde-woo-notices__info-link-text-hover:var(--sky-500);--bde-woo-notices__success-background:var(--emerald-100);--bde-woo-notices__success-text:var(--emerald-700);--bde-woo-notices__success-link-text:var(--emerald-700);--bde-woo-notices__success-link-text-hover:var(--emerald-700);--bde-woo-sale-badge__border-radius:2px;--bde-woo-sale-badge__padding:4px 8px;--bde-woo-ratings__star-color:var(--yellow-500);--bde-woo-ratings__star-size:18px;--bde-woo-ratings__filled-star-svg:url('data:image/svg+xml;utf8,');--bde-woo-ratings__empty-star-svg:url('data:image/svg+xml;utf8,');--bde-woo-product-images__border-radius:4px;--bde-woo-product-images__border-width:0px;--bde-woo-product-images__border-color:var(--grey-300);--bde-woo-wrappers__background-color:var(--white);--bde-woo-wrappers__border-radius:4px;--bde-woo-wrappers__border-color:var(--grey-300);--bde-woo-wrappers__border-width:1px;--bde-woo-wrappers__shadow:rgba(0,0,0,.05) 0 1px 3px,rgba(0,0,0,.05) 0 1px 2px;--bde-woo-tables__header-color:var(--grey-100);--bde-woo-tables__background-color:var(--white);--bde-woo-tables__border-radius:4px;--bde-woo-tables__border-width:1px;--bde-woo-widgets__chip-background-color:transparent;--bde-woo-widgets__chip-background-color-hover:var(--indigo-50);--bde-woo-widgets__chip-text-color:inherit;--bde-woo-widgets__handle-border-color:var(--grey-300);--bde-woo-widgets__handle-background-color:var(--white);--bde-woo-widgets__handle-background-color-hover:var(--white);--bde-woo-widgets__handle-shadow:rgba(0,0,0,.05) 0 1px 3px,rgba(0,0,0,.05) 0 1px 2px;--bde-woo-widgets__handle-shadow-hover:var(--grey-300) 0 0 4px;--bde-woo-widgets__remove-item-from-cart-color:var(--grey-450);--bde-woo-select2__active-item-background-color:var(--indigo-50);--bde-woo-gallery__zoom-icon-shadow:rgba(0,0,0,.05) 0 1px 3px,rgba(0,0,0,.05) 0 1px 2px;--bde-woo-payment-box-background-color:var(--grey-100);--bde-woo-payment-box-border-color:var(--grey-200);--bde-woo-payment-box-border-width:1px;--bde-woo-quicklook-button-icon:url(/wp-content/uploads/breakdance/css/icons/eye.svg);--bde-woo-quicklook-button-background-color:none;--bde-woo-quicklook-button-icon-size:20px;--bde-woo-quicklook-button-backdrop-color:rgba(0,0,0,.15);--bde-woo-quicklook-button-backdrop-opacity:.7;--bde-woo-quicklook-modal-background-color:var(--white);--bde-woo-quicklook-overlay-color:rgba(0,0,0,.7);--bde-woo-quicklook-close-button-size:2em;--bde-woo-quicklook-arrow-size:1em;--bde-woo-quicklook-arrow-color:var(--white);--bde-woo-swatch-space-between-options:10px;--bde-woo-swatch-padding:7px;--bde-woo-swatch-color-width:30px;--bde-woo-swatch-color-height:30px;--bde-woo-swatch-border:1px solid var(--grey-200);--bde-woo-swatch-border-color-hover:var(--grey-400);--bde-woo-swatch-shadow:none;--bde-woo-swatch-shadow-hover:none;--bde-woo-swatch-background:var(--white);--bde-woo-swatch-background-hover:var(--grey-50);--bde-woo-swatch-color-padding:2px;--bde-woo-swatch-tooltip-color:var(--white);--bde-woo-swatch-tooltip-background:var(--grey-900);--bde-woo-swatch-tooltip-padding:7px;--bde-woo-swatch-space-after-label:8px;--bde-woo-responsive__stack:row}:root{--bde-links-color:var(--bde-palette-orange-59d0709f-53a9-485b-af53-1d4d3c953a6b-3);--bde-links-color-hover:var(--bde-palette-orange-59d0709f-53a9-485b-af53-1d4d3c953a6b-3);--bde-button-primary-background-color:var(--bde-brand-primary-color);--bde-button-primary-background-color-hover:var(--bde-brand-primary-color-hover);--bde-button-secondary-border-color:var(--bde-brand-primary-color);--bde-button-secondary-border-color-hover:var(--bde-brand-primary-color);--bde-button-secondary-text-color:var(--bde-brand-primary-color);--bde-button-secondary-background-color-hover:var(--bde-brand-primary-color);--bde-button-text-text-color:var(--bde-links-color);--bde-button-text-text-color-hover:var(--bde-links-color-hover);--bde-button-font-size:var(--bde-body-font-size);--bde-form-font-size:var(--bde-body-font-size);--bde-form-input-border-top-left-radius:var(--bde-form-input-border-radius);--bde-form-input-border-top-right-radius:var(--bde-form-input-border-radius);--bde-form-input-border-bottom-left-radius:var(--bde-form-input-border-radius);--bde-form-input-border-bottom-right-radius:var(--bde-form-input-border-radius);--bde-form-input-border-top:var(--bde-form-input-border-width) solid var(--bde-form-input-border-color);--bde-form-input-border-right:var(--bde-form-input-border-width) solid var(--bde-form-input-border-color);--bde-form-input-border-bottom:var(--bde-form-input-border-width) solid var(--bde-form-input-border-color);--bde-form-input-border-left:var(--bde-form-input-border-width) solid var(--bde-form-input-border-color);--bde-form-label-color:var(--bde-headings-color);--bde-form-input-focused-border-color:var(--bde-brand-primary-color);--bde-form-input-focused-shadow:var(--bde-brand-primary-color) 0 0 2px;--bde-form-checkbox-selected-color:var(--bde-brand-primary-color);--bde-z-index-lightbox:1100;--bde-z-index-popup:1050;--bde-z-index-modal:1000;--bde-z-index-modal-backdrop:calc(var(--bde-z-index-modal) - 1);--bde-z-index-high:300;--bde-z-index-medium:200;--bde-z-index-low:100;--bde-z-index-sticky:10;--bde-z-index-minicart:var(--bde-z-index-modal);--bde-z-index-minicart-backdrop:var(--bde-z-index-modal-backdrop);--bde-z-index-menu-dropdown:var(--bde-z-index-modal);--bde-z-index-menu-mobile:var(--bde-z-index-modal);--bde-z-index-menu-backdrop:var(--bde-z-index-modal-backdrop);--bde-z-index-search-fullscreen:var(--bde-z-index-modal);--bde-z-index-back-to-top:var(--bde-z-index-high);--bde-z-index-scroll-progress:var(--bde-z-index-high);--bde-z-index-header-sticky:var(--bde-z-index-medium);--bde-z-index-header-overlay:calc(var(--bde-z-index-header-sticky) - 1);--bde-z-index-social-share-buttons:var(--bde-z-index-low);--bde-woo-base-text-color:var(--bde-body-text-color);--bde-woo-base-headings-color:var(--bde-headings-color);--bde-woo-base-primary-color:var(--bde-brand-primary-color);--bde-woo-base-primary-color-hover:var(--bde-brand-primary-color-hover);--bde-woo-base-extra-small-gaps:calc(var(--bde-woo-base-small-gaps)/var(--bde-woo-base-ratio));--bde-woo-base-small-gaps:calc(var(--bde-woo-base-space)/var(--bde-woo-base-ratio));--bde-woo-base-standard-gaps:var(--bde-woo-base-space);--bde-woo-base-medium-gaps:calc(var(--bde-woo-base-space)*var(--bde-woo-base-ratio));--bde-woo-base-big-gaps:calc(var(--bde-woo-base-medium-gaps)*var(--bde-woo-base-ratio));--bde-woo-base-large-gaps:calc(var(--bde-woo-base-big-gaps)*var(--bde-woo-base-ratio));--bde-woo-base-extra-large-gaps:calc(var(--bde-woo-base-large-gaps)*var(--bde-woo-base-ratio));--bde-woo-typography-ratio:var(--bde-font-size-ratio);--bde-woo-typography__size-small:calc(var(--bde-woo-typography__size-standard)/var(--bde-woo-typography-ratio));--bde-woo-typography__size-small-font-family:var(--bde-body-font-family);--bde-woo-typography__size-standard:var(--bde-body-font-size);--bde-woo-typography__size-standard-font-family:var(--bde-body-font-family);--bde-woo-typography__size-medium:calc(var(--bde-woo-typography__size-standard)*var(--bde-woo-typography-ratio));--bde-woo-typography__size-medium-font-family:var(--bde-heading-font-family);--bde-woo-typography__size-large:calc(var(--bde-woo-typography__size-medium)*var(--bde-woo-typography-ratio));--bde-woo-typography__size-large-font-family:var(--bde-heading-font-family);--bde-woo-typography__size-extra-large:calc(var(--bde-woo-typography__size-large)*var(--bde-woo-typography-ratio));--bde-woo-typography__size-extra-large-font-family:var(--bde-heading-font-family);--bde-woo-buttons-and-links__text-link-color:var(--bde-woo-base-primary-color);--bde-woo-buttons-and-links__text-link-color-hover:var(--bde-woo-base-primary-color-hover);--bde-woo-buttons-and-links__nav-link-color:var(--bde-woo-base-text-color);--bde-woo-buttons-and-links__nav-link-color-hover:var(--bde-woo-base-text-on-primary-color);--bde-woo-buttons-and-links__nav-link-color-active:var(--bde-woo-base-primary-color);--bde-woo-forms__spacing-after-label:var(--bde-form-after-label);--bde-woo-forms__spacing-between-fields:var(--bde-form-gap);--bde-woo-forms__spacing-between-columns:var(--bde-woo-base-extra-large-gaps);--bde-woo-forms__labels-color:var(--bde-form-label-color);--bde-woo-forms__inputs-background-color:var(--bde-form-input-background-color);--bde-woo-forms__inputs-text-color:var(--bde-form-text-color);--bde-woo-forms__inputs-placeholder-color:var(--bde-form-input-placeholder-color);--bde-woo-forms__inputs-border-color:var(--bde-form-input-border-color);--bde-woo-forms__inputs-border-width:var(--bde-form-input-border-width);--bde-woo-forms__inputs-border-radius:var(--bde-form-input-border-top-left-radius) var(--bde-form-input-border-top-right-radius) var(--bde-form-input-border-bottom-right-radius) var(--bde-form-input-border-bottom-left-radius);--bde-woo-forms__inputs-background-color-focused:var(--bde-form-input-focused-background-color);--bde-woo-forms__inputs-border-color-focused:var(--bde-form-input-focused-border-color);--bde-woo-forms__inputs-shadow-focused:var(--bde-form-input-focused-shadow);--bde-woo-forms__inputs-shadow:var(--bde-form-input-input-shadow);--bde-woo-forms__inputs-select2-hover-item:var(--bde-woo-base-primary-color);--bde-woo-forms__labels-required-color:var(--bde-form-label-required-color);--bde-woo-forms__labels-required-size:var(--bde-form-label-required-size);--bde-woo-forms__labels-required-nudge-x:var(--bde-form-label-required-nudge-x);--bde-woo-forms__labels-required-nudge-y:var(--bde-form-label-required-nudge-y);--bde-woo-tables__border-color:var(--bde-woo-base-border-color);--bde-woo-sale-badge__background-color:var(--bde-woo-base-primary-color);--bde-woo-sale-badge__text-color:var(--bde-woo-base-text-on-primary-color);--bde-woo-sale-badge__font-weight:var(--bde-woo-typography-font-weight-heavy);--bde-woo-sale-badge__font-size:var(--bde-woo-typography__size-standard);--bde-woo-widgets__chip-text-color-hover:var(--bde-woo-buttons-and-links__text-link-color);--bde-woo-widgets__handle-border-color-hover:var(--bde-woo-base-primary-color);--bde-woo-notices__padding-left:calc(var(--bde-woo-notices__padding) + var(--bde-woo-notices__icon-size) + (var(--bde-woo-notices__icon-size)/2));--bde-woo-quicklook-button-text-color:var(--bde-button-primary-text-color);--bde-woo-quicklook-button-background-color-hover:var(--bde-woo-quicklook-button-background-color);--bde-woo-quicklook-button-icon-spacing:var(--bde-woo-base-standard-gaps);--bde-woo-quicklook-close-button-color:var(--bde-woo-base-headings-color);--bde-woo-quicklook-arrow-color-hover:var(--bde-woo-quicklook-arrow-color);--bde-woo-quicklook-arrow-background-color:var(--bde-brand-primary-color);--bde-woo-quicklook-arrow-background-color-hover:var(--bde-woo-quicklook-arrow-background-color);--bde-woo-swatch-space-between-items:var(--bde-woo-base-medium-gaps);--bde-woo-swatch-background-selected:var(--bde-woo-swatch-background-hover);--bde-woo-swatch-border-color-selected:var(--bde-woo-swatch-border-color-hover);--bde-woo-swatch-shadow-selected:var(--bde-woo-swatch-shadow-hover);--bde-woo-swatch-color-background:var(--bde-woo-swatch-background)}:root{--bde-base-font-size:18px}.breakdance .button-atom{display:inline-flex;align-items:center;justify-content:center;vertical-align:middle;appearance:none;box-sizing:border-box;margin:0;border:0;padding:0;background-color:transparent;font-size:var(--bde-button-font-size);line-height:var(--bde-button-line-height);transform:translate(0,0);max-width:100%;width:var(--bde-button-width)}.breakdance .button-atom--primary{text-align:center;font-weight:var(--bde-button-font-weight);text-decoration:none;padding:var(--bde-button-padding-base);border-radius:var(--bde-button-border-radius);border-width:var(--bde-button-border-width);border-style:solid;border-color:transparent;overflow:hidden}.breakdance .button-atom--primary{color:var(--bde-button-primary-text-color);background:var(--bde-button-primary-background-color);border-color:var(--bde-button-primary-border-color)}.breakdance *,.breakdance *:before,.breakdance *:after{box-sizing:border-box}.breakdance img{max-width:100%;height:auto}.breakdance figure{width:100%;margin-left:0;margin-right:0}.breakdance-rich-text-styles>*:first-child{margin-top:0}.breakdance{background-color:var(--bde-background-color);color:var(--bde-body-text-color)}.breakdance h1{color:var(--bde-headings-color)}.breakdance a{color:var(--bde-links-color)}.breakdance .button-atom--primary{--bde-button-primary-border-color:transparent;--bde-button-primary-border-color-hover:transparent;--bde-button-primary-text-color:#fff;--bde-button-primary-text-color-hover:#fff;--bde-button-primary-background-color:#f86f21;--bde-button-primary-background-color-hover:#f86f21;border-radius:9999px;padding-top:20px;padding-right:30px;padding-bottom:20px;padding-left:30px}.breakdance{font-family:var(--bde-body-font-family);font-size:var(--bde-body-font-size)}.breakdance h1{font-family:var(--bde-heading-font-family)}.breakdance h1{font-size:var(--bde-h1-font-size)}.breakdance{color:#84827d;font-family:"Work Sans",sans-serif;font-size:18px;font-weight:500}.breakdance a{color:var(--bde-palette-orange-59d0709f-53a9-485b-af53-1d4d3c953a6b-3)}:root{--preset-id-032a13e5-5911-4637-afe7-449e8eddd86d-font-family:"Work Sans",sans-serif;--preset-id-032a13e5-5911-4637-afe7-449e8eddd86d-font-size:18px;--preset-id-032a13e5-5911-4637-afe7-449e8eddd86d-font-weight:600;--preset-id-032a13e5-5911-4637-afe7-449e8eddd86d-line-height:1.6em}@media (max-width:479px){:root{--preset-id-032a13e5-5911-4637-afe7-449e8eddd86d-font-family:"Work Sans",sans-serif;--preset-id-032a13e5-5911-4637-afe7-449e8eddd86d-font-size:20px;--preset-id-032a13e5-5911-4637-afe7-449e8eddd86d-font-weight:600}}.breakdance .bde-section-4224-100 .section-container{align-items:center;text-align:center;justify-content:center}.breakdance .bde-section-4224-100{background-color:var(--bde-background-color);background-size:cover;background-repeat:no-repeat;background-position:center bottom}.breakdance .bde-section-4224-100>.section-background-overlay{background-color:#333333CF}.breakdance .bde-section-4224-100 .section-container{min-height:80vh}.breakdance .bde-section-4224-100 .section-container{padding-bottom:120px;padding-top:120px}.breakdance .bde-section-4224-100{margin-top:-155px}.breakdance .bde-image-4224-101{margin-top:175px}.breakdance .bde-text-4224-102{width:720px;color:#fff;font-size:23px;font-weight:700;text-transform:uppercase;margin-top:20px;margin-bottom:56px}.breakdance .bde-heading-4224-103{color:var(--bde-background-color);margin-bottom:75px}.breakdance .bde-header-builder-14-177{background:#642EDA00;--bde-header-width:100%}.breakdance .bde-header-builder-14-177 .bde-header-builder__header-builder-border-top{height:1px;background:var(--bd-palette-color-4)}.breakdance .bde-header-builder-14-177 .bde-header-builder__container{padding-bottom:20px;padding-top:20px}.breakdance .bde-header-builder-14-177{z-index:1}.breakdance .bde-header-builder-14-177 .breakdance-menu{--link-alignment:start}@media (max-width:479px){.breakdance .bde-header-builder-14-177{--bde-header-width:100%}}.breakdance .bde-div-14-178{gap:28px;flex-wrap:wrap;flex-direction:row;align-items:center}@media (max-width:767px){.breakdance .bde-div-14-178{flex-direction:column}}.breakdance .bde-container-link-14-179{opacity:.9}.breakdance .bde-image-14-180{width:320px}.breakdance .bde-image-14-180 .breakdance-image-object{width:100%;height:auto}@media (max-width:479px){.breakdance .bde-image-14-180{margin-top:-10px;width:250px}.breakdance .bde-image-14-180 .breakdance-image-object{width:100%;height:auto}}@media (max-width:1023px){.breakdance .bde-div-14-194{align-items:center;text-align:center}}@media (max-width:767px){.breakdance .bde-div-14-194{align-items:center;text-align:center}}@media (max-width:479px){.breakdance .bde-div-14-194{flex-wrap:wrap;flex-direction:row;align-items:center;justify-content:flex-end;flex-direction:column}}@media (max-width:1023px){.breakdance .bde-menu-14-181 .breakdance-menu{--mobile-offset-y:52px;--menu-background:#fff;--toggle-layer-height:3px;--toggle-layer-color:#fff;--toggle-layer-border-radius:2px;--link-color-active:var(--bde-palette-dark-grey-6b584f8c-aa83-4067-ae5d-4646f3bfae41-6)}}@media (min-width:1024px){.breakdance .bde-menu-14-181 .breakdance-menu{--links-gap:24px;--link-color:#fff;--link-color-hover:var(--bde-palette-orange-59d0709f-53a9-485b-af53-1d4d3c953a6b-3);--link-padding-top:8px;--link-padding-right:16px;--link-padding-bottom:8px;--link-padding-left:16px;--link-effect-color:#D1D5DB40;--link-effect-color-hover:#D1D5DB40;--link-effect-radius:6px;--dropdown-custom-offset-y:0px}.breakdance .bde-menu-14-181 .breakdance-menu-link{color:#fff}}@media (max-width:1023px){.breakdance .bde-menu-14-181 .breakdance-menu{--link-color:var(--bde-palette-dark-grey-6b584f8c-aa83-4067-ae5d-4646f3bfae41-6)}.breakdance .bde-menu-14-181 .breakdance-menu-link{color:var(--bde-palette-dark-grey-6b584f8c-aa83-4067-ae5d-4646f3bfae41-6)}.breakdance .bde-menu-14-181 .breakdance-menu .breakdance-dropdown-column__title{color:var(--bde-palette-dark-grey-6b584f8c-aa83-4067-ae5d-4646f3bfae41-6)}.breakdance .bde-menu-14-181 .breakdance-dropdown-link{color:var(--bde-palette-dark-grey-6b584f8c-aa83-4067-ae5d-4646f3bfae41-6)}.breakdance .bde-menu-14-181 .breakdance-menu{--links-gap:0;--dropdown-link-icon-display:none;--dropdown-link-description-display:none;--dropdown-links-gap:var(--gap-none)}.breakdance .bde-menu-14-181 .breakdance-menu-list{align-items:stretch;background-color:var(--menu-background);display:none;flex-direction:column;left:var(--mobile-offset-x);max-height:var(--menu-max-height);overflow-y:auto;position:absolute;top:var(--mobile-offset-y,100%);width:100vw;z-index:var(--bde-z-index-menu-mobile)}.breakdance .bde-menu-14-181 .breakdance-menu-list>.bde-button{border-top:var(--link-border);justify-content:var(--link-alignment);margin-left:0;padding:10px 15px}.breakdance .bde-menu-14-181 .breakdance-menu-list>.bde-button .button-atom{width:var(--bde-button-width,100%)}.breakdance .bde-menu-14-181 .breakdance-menu-list>:last-child{border-bottom:var(--link-border)}.breakdance .bde-menu-14-181 .breakdance-menu .breakdance-menu-link{border-top:var(--link-border);outline-offset:-1px;padding:var(--mobile-link-padding-top) var(--mobile-link-padding-right) var(--mobile-link-padding-bottom) var(--mobile-link-padding-left)}.breakdance .bde-menu-14-181 .breakdance-menu-link-arrow{border-top:var(--link-border);bottom:0;position:absolute;right:0;top:0}.breakdance .bde-menu-14-181 .breakdance-dropdown-floater{transform:none;visibility:visible}.breakdance .bde-menu-14-181 .breakdance-dropdown-body{background-color:var(--link-background-color);border-radius:0;border-top:var(--link-border);box-shadow:none;flex-direction:column}.breakdance .bde-menu-14-181 .breakdance-dropdown--custom .breakdance-dropdown-floater{width:auto}.breakdance .bde-menu-14-181 .breakdance-dropdown-section{--dropdown-section-padding:0;--dropdown-section-gap:var(--gap-none)}.breakdance .bde-menu-14-181 .breakdance-dropdown-section--additional{background-color:transparent;border-top:var(--link-border)}.breakdance .bde-menu-14-181 .breakdance-dropdown-columns{--dropdown-columns-stack:column;--dropdown-columns-gap:var(--gap-none)}.breakdance .bde-menu-14-181 .breakdance-dropdown-column{gap:var(--gap-none)}.breakdance .bde-menu-14-181 .breakdance-dropdown-column+.breakdance-dropdown-column{border-top:var(--link-border)}.breakdance .bde-menu-14-181 .breakdance-menu--collapse .breakdance-dropdown-column--collapsible{gap:var(--gap-none)}.breakdance .bde-menu-14-181 .breakdance-menu--collapse .breakdance-dropdown-column--collapsible .breakdance-dropdown-item:first-child{border-top:var(--link-border)}.breakdance .bde-menu-14-181 .breakdance-menu--collapse .breakdance-dropdown-column--collapsible .breakdance-dropdown-column__title{outline-offset:-1px}.breakdance .bde-menu-14-181 .breakdance-menu--collapse .breakdance-dropdown-column--collapsible .breakdance-dropdown-links:not(.is-visible):not(.is-collapsing){height:0;overflow:hidden;visibility:hidden}.breakdance .bde-menu-14-181 .breakdance-dropdown-column__title{font-weight:500;justify-content:var(--link-alignment);padding:var(--mobile-link-level-2-padding-top) var(--mobile-link-level-2-padding-right) var(--mobile-link-level-2-padding-bottom) var(--mobile-link-level-2-padding-left);white-space:normal}.breakdance .bde-menu-14-181 .breakdance-menu--collapse .breakdance-dropdown-column--collapsible .breakdance-dropdown-column__title:after{display:block}.breakdance .bde-menu-14-181 .breakdance-dropdown-item+.breakdance-dropdown-item{border-top:var(--link-border)}.breakdance .bde-menu-14-181 .breakdance-menu .breakdance-dropdown-link{justify-content:var(--link-alignment);outline-offset:-1px;padding:var(--mobile-link-level-3-padding-top) var(--mobile-link-level-3-padding-right) var(--mobile-link-level-3-padding-bottom) var(--mobile-link-level-3-padding-left);white-space:normal}.breakdance .bde-menu-14-181 .breakdance-menu-toggle{display:flex}.breakdance .bde-menu-14-181{margin-top:20px}}@media (max-width:479px){@media (max-width:1023px){.breakdance .bde-menu-14-181 .breakdance-menu{--link-color:var(--bde-palette-dark-grey-6b584f8c-aa83-4067-ae5d-4646f3bfae41-6)}.breakdance .bde-menu-14-181 .breakdance-menu-link{color:var(--bde-palette-dark-grey-6b584f8c-aa83-4067-ae5d-4646f3bfae41-6)}.breakdance .bde-menu-14-181 .breakdance-menu .breakdance-dropdown-column__title{color:var(--bde-palette-dark-grey-6b584f8c-aa83-4067-ae5d-4646f3bfae41-6)}.breakdance .bde-menu-14-181 .breakdance-dropdown-link{color:var(--bde-palette-dark-grey-6b584f8c-aa83-4067-ae5d-4646f3bfae41-6)}}.breakdance .bde-menu-14-181{margin-top:10px}}@media (min-width:1024px){.breakdance .bde-menu-dropdown-14-182 .breakdance-dropdown{--dropdown-background-color:var(--bde-palette-dark-grey-6b584f8c-aa83-4067-ae5d-4646f3bfae41-6);--dropdown-custom-width:800px;--dropdown-sections-stack:row;--dropdown-section-padding:24px}.breakdance .bde-menu-dropdown-14-182 .breakdance-dropdown-section:nth-child(1) .breakdance-dropdown-column:nth-child(1) .breakdance-dropdown-item:nth-child(1){--dropdown-link-icon-color:var(--bde-background-color);--dropdown-link-icon-size:28px;--dropdown-link-icon-alignment:flex-start;--dropdown-link-icon-y:4px;--dropdown-link-icon-background:var(--bde-brand-primary-color);--dropdown-link-icon-radius:6px;--dropdown-link-icon-padding:12px}.breakdance .bde-menu-dropdown-14-182 .breakdance-dropdown-section:nth-child(1) .breakdance-dropdown-column:nth-child(2) .breakdance-dropdown-item:nth-child(1){--dropdown-link-icon-color:var(--bde-background-color);--dropdown-link-icon-size:28px;--dropdown-link-icon-alignment:flex-start;--dropdown-link-icon-y:4px;--dropdown-link-icon-background:var(--bde-brand-primary-color);--dropdown-link-icon-radius:6px;--dropdown-link-icon-padding:12px}.breakdance .bde-menu-dropdown-14-182 .breakdance-dropdown-section:nth-child(1) .breakdance-dropdown-column:nth-child(3) .breakdance-dropdown-item:nth-child(1){--dropdown-link-icon-color:var(--bde-background-color);--dropdown-link-icon-size:28px;--dropdown-link-icon-alignment:flex-start;--dropdown-link-icon-y:4px;--dropdown-link-icon-background:var(--bde-brand-primary-color);--dropdown-link-icon-radius:6px;--dropdown-link-icon-padding:12px}.breakdance .bde-menu-dropdown-14-182 .breakdance-dropdown-section:nth-child(1) .breakdance-dropdown-column:nth-child(4) .breakdance-dropdown-item:nth-child(1){--dropdown-link-icon-color:var(--bde-background-color);--dropdown-link-icon-size:28px;--dropdown-link-icon-alignment:flex-start;--dropdown-link-icon-y:4px;--dropdown-link-icon-background:var(--bde-brand-primary-color);--dropdown-link-icon-radius:6px;--dropdown-link-icon-padding:12px}.breakdance .bde-menu-dropdown-14-182 .breakdance-dropdown{--dropdown-columns-gap:12px;--dropdown-column-title-spacing:0px;--dropdown-columns-stack:column}.breakdance .bde-menu-dropdown-14-182 .breakdance-dropdown .breakdance-dropdown-column__title{color:#fff;text-decoration-color:var(--bde-palette-orange-59d0709f-53a9-485b-af53-1d4d3c953a6b-3);text-decoration-line:underline;text-transform:uppercase}.breakdance .bde-menu-dropdown-14-182 .breakdance-dropdown{--dropdown-links-gap:4px;--dropdown-link-background-color-hover:var(--bd-palette-color-1);--dropdown-link-icon-spacing:17px}.breakdance .bde-menu-dropdown-14-182 .breakdance-dropdown .breakdance-dropdown-link{padding:10px 16px;border-radius:6px}.breakdance .bde-menu-dropdown-14-182 .breakdance-dropdown .breakdance-dropdown-link__text{color:#fff;font-weight:700}.breakdance .bde-menu-dropdown-14-182 .breakdance-dropdown .breakdance-dropdown-link__description{color:var(--bde-palette-white-cff87cd8-a9df-41f1-9027-98896e727843-5);font-family:"PT Sans",sans-serif;font-size:14px;font-weight:400;line-height:1.6em;letter-spacing:0px;word-spacing:0px}.breakdance .bde-menu-dropdown-14-182 .breakdance-dropdown .breakdance-dropdown-section--additional{--dropdown-section-dark-background:var(--bd-palette-color-1);--dropdown-section-padding:24px}.breakdance .bde-menu-dropdown-14-182 .breakdance-dropdown .breakdance-dropdown-section--additional{--dropdown-columns-gap:0px;--dropdown-column-title-spacing:0px;--dropdown-columns-stack:column}.breakdance .bde-menu-dropdown-14-182 .breakdance-dropdown .breakdance-dropdown-section--additional .breakdance-dropdown-link__text{color:#fff}.breakdance .bde-menu-dropdown-14-182 .breakdance-dropdown .breakdance-dropdown-section--additional .breakdance-dropdown-link__description{font-family:"PT Sans",sans-serif;font-size:14px;font-weight:400;line-height:28px;letter-spacing:0px;word-spacing:0px}}@media (max-width:1023px){@media (min-width:1024px){.breakdance .bde-menu-dropdown-14-182 .breakdance-dropdown .breakdance-dropdown-link__text{color:var(--bde-palette-dark-grey-6b584f8c-aa83-4067-ae5d-4646f3bfae41-6)}}}@media (min-width:1024px){.breakdance .bde-menu-dropdown-14-198 .breakdance-dropdown{--dropdown-background-color:var(--bde-palette-dark-grey-6b584f8c-aa83-4067-ae5d-4646f3bfae41-6);--dropdown-custom-width:800px;--dropdown-sections-stack:row;--dropdown-section-padding:24px}.breakdance .bde-menu-dropdown-14-198 .breakdance-dropdown-section:nth-child(1) .breakdance-dropdown-column:nth-child(1) .breakdance-dropdown-item:nth-child(1){--dropdown-link-icon-color:var(--bde-background-color);--dropdown-link-icon-size:28px;--dropdown-link-icon-alignment:flex-start;--dropdown-link-icon-y:4px;--dropdown-link-icon-background:var(--bde-brand-primary-color);--dropdown-link-icon-radius:6px;--dropdown-link-icon-padding:12px}.breakdance .bde-menu-dropdown-14-198 .breakdance-dropdown{--dropdown-columns-gap:12px;--dropdown-column-title-spacing:0px;--dropdown-columns-stack:column}.breakdance .bde-menu-dropdown-14-198 .breakdance-dropdown{--dropdown-links-gap:4px;--dropdown-link-background-color-hover:var(--bd-palette-color-1);--dropdown-link-icon-spacing:17px}.breakdance .bde-menu-dropdown-14-198 .breakdance-dropdown .breakdance-dropdown-link{padding:10px 16px;border-radius:6px}.breakdance .bde-menu-dropdown-14-198 .breakdance-dropdown .breakdance-dropdown-link__text{color:#fff;font-weight:700}.breakdance .bde-menu-dropdown-14-198 .breakdance-dropdown .breakdance-dropdown-link__description{color:var(--bde-palette-white-cff87cd8-a9df-41f1-9027-98896e727843-5);font-family:"PT Sans",sans-serif;font-size:14px;font-weight:400;line-height:1.6em;letter-spacing:0px;word-spacing:0px}.breakdance .bde-menu-dropdown-14-198 .breakdance-dropdown .breakdance-dropdown-section--additional{--dropdown-section-dark-background:var(--bd-palette-color-1);--dropdown-section-padding:24px}.breakdance .bde-menu-dropdown-14-198 .breakdance-dropdown .breakdance-dropdown-section--additional{--dropdown-columns-gap:0px;--dropdown-column-title-spacing:0px;--dropdown-columns-stack:column}.breakdance .bde-menu-dropdown-14-198 .breakdance-dropdown .breakdance-dropdown-section--additional .breakdance-dropdown-link__text{color:#fff}.breakdance .bde-menu-dropdown-14-198 .breakdance-dropdown .breakdance-dropdown-section--additional .breakdance-dropdown-link__description{font-family:"PT Sans",sans-serif;font-size:14px;font-weight:400;line-height:28px;letter-spacing:0px;word-spacing:0px}}@media (max-width:1023px){@media (min-width:1024px){.breakdance .bde-menu-dropdown-14-198 .breakdance-dropdown .breakdance-dropdown-link__text{color:var(--bde-palette-dark-grey-6b584f8c-aa83-4067-ae5d-4646f3bfae41-6)}}}@media (min-width:1120px){.breakdance .bde-button-14-195{display:none}}@media (max-width:1119px) and (min-width:1024px){.breakdance .bde-button-14-195{display:none}}@media (min-width:1120px){.breakdance .bde-text-14-193{display:none}}@media (max-width:1119px) and (min-width:1024px){.breakdance .bde-text-14-193{display:none}}@media (max-width:1023px){.breakdance .bde-text-14-193{color:#fff}}@media (max-width:767px){.breakdance .bde-text-14-193{color:#fff}}@media (max-width:479px){.breakdance .bde-text-14-193{color:#fff}}.breakdance .bde-div-14-186{gap:16px;flex-wrap:wrap;flex-direction:row;align-items:center}@media (max-width:1023px) and (min-width:768px){.breakdance .bde-div-14-186{display:none}}@media (max-width:767px) and (min-width:480px){.breakdance .bde-div-14-186{display:none}}@media (max-width:479px){.breakdance .bde-div-14-186{display:none}}@media (max-width:479px){.breakdance .bde-div-14-186{flex-direction:column}}@media (max-width:1023px) and (min-width:768px){.breakdance .bde-button-14-187{display:none}}@media (max-width:767px) and (min-width:480px){.breakdance .bde-button-14-187{display:none}}@media (max-width:479px){.breakdance .bde-button-14-187{display:none}}@media (max-width:479px){.breakdance .bde-button-14-187{display:flex}}.breakdance .bde-section-4224-100{background-color:var(--bde-background-color);background-image:url(https://alphaomegapainting.ca/wp-content/uploads/2023/09/cost-to-paint-a-1000-sq-ft-home-vancouver_1694812227598-1.jpeg);background-size:cover;background-repeat:no-repeat;background-position:center bottom}.breakdance .bde-section-4224-100>.section-background-overlay{background-color:#333333CF}
Understanding Industrial Facility Painting Services
Industrial facility painting services encompass a range of specialized services tailored to the maintenance, protection, and aesthetic enhancement of industrial properties. From the preparation of surfaces to protective coatings and finishes, industrial painting contractors provide a comprehensive solution for facilities in various industries.
Industrial facility painting is focused on the application of specialized paints, coatings, and treatments to industrial structures, equipment, and environments. This typically means working with materials and machinery that must withstand heavy wear and tear, extreme temperatures, and harsh environmental conditions.
The scope of industrial painting services extends beyond merely painting walls and ceilings. It may also include applying floor coatings and sealants, painting large-scale equipment, and corrosion control treatments for steel structures.
Some common areas and elements that may require industrial facility painting services include:
Industrial painting services play a critical role in the overall maintenance and management of industrial facilities. Some of the key benefits of industrial painting for facility maintenance include:
Surface Protection: Industrial painting helps to protect surfaces from harsh environments, chemical exposure, and wear-and-tear, increasing the durability and lifespan of industrial buildings and equipment.
Corrosion Control: The application of specialized coatings inhibits the corrosion of metal surfaces, preventing structural damage and costly repairs over time.
Safety: Visible and colour-coded systems for industrial facilities can help employees to identify and avoid hazards, reducing incidents and minimizing potential safety risks.
Cleanliness: The right paint and coating systems can help to facilitate hygiene and cleanliness, ensuring that facilities meet regulatory standards, particularly in industries with strict sanitary requirements such as food processing and pharmaceuticals.
Aesthetic Enhancement: A well-painted facility creates a positive work environment, supports a professional image, and can boost employee morale and productivity.
Selecting the right industrial painting service is crucial for achieving the desired results and ensuring a smooth, efficient painting process. Some key factors to consider when choosing an industrial painting contractor include:
Experience and Expertise: Seek out painting professionals with a proven track record in the specific industry or type of facility concerned, as they will have the necessary knowledge and skills to ensure the best results.
Licensing and Certifications: Verify that the contractor is appropriately licensed, insured, and certified in order to guarantee compliance with legal and safety requirements.
Preparation and Planning: Look for painting providers that emphasize thorough surface preparation and project planning in order to ensure a smooth, efficient process and long-lasting results.
Quality Materials and Techniques: High-quality paint, coatings, and equipment make a significant difference in the durability and appearance of an industrial facility. A reputable contractor should use premium materials and stay up-to-date with industry trends and techniques.
Communication and Collaboration: A provider who is open to communication and collaboration can help to build a strong working relationship and ensure that the project is completed in a timely, satisfactory manner.
By thoroughly researching and considering options, industrial facility managers can find the right industrial painting service to maintain and protect their valuable assets.
Industrial facility painting is a specialized service designed to meet the unique requirements of various industries. Different types of industrial facilities have specific painting needs depending on their operation processes, environmental regulations, and safety measures. In this article, we discuss the various types of industrial facility painting services available in the market.
Manufacturing and production facilities need painting services that can withstand the rigorous, high-intensity operations that often produce extensive wear and tear. These facilities typically require painting solutions that offer long-lasting protection against corrosion, extreme temperatures, and harsh chemical exposure. Some services that cater to manufacturing and production facilities include epoxy floor coatings, protective steel coatings, and intumescent coatings for fire protection.
Warehouses and storage facilities are essential for businesses that need to store raw materials, goods, or products. Proper painting is vital in maintaining a clean and organized environment for efficient inventory management. Among other things, painting services for this type of facility involve applying durable floor coatings, painting safety and aisle lines, and painting exterior walls for protection against harsh weather conditions.
Food processing plants and facilities require painting services that adhere to strict sanitation and hygiene standards. Painting solutions in these facilities should be able to resist bacterial and fungal growth and protect surfaces from harsh cleaning chemicals. Some products and services relevant to food processing plants include antimicrobial coatings, USDA-approved coatings, and slip-resistant floor coatings.
Chemical plants and refineries deal with hazardous and corrosive materials daily. Therefore, their painting needs revolve around ensuring the facilities remain safe and free from corrosion or degradation. Specialized painting services for chemical plants and refineries include corrosion-resistant coatings, high-temperature coatings, and industrial coatings specifically designed to protect various types of equipment, structures, and surfaces.
Power plants and utilities facilities require painting services that can protect surfaces from extreme temperatures, weather conditions, and wear caused by high-energy operations. Some of the painting services tailored for these facilities include high-performance coatings for boiler systems, storage tanks, cooling towers, and pipeline systems.
Pharmaceutical manufacturing facilities must maintain high standards of cleanliness and sanitation, as well as meet stringent FDA regulations. As a result, these facilities require specialized painting services that involve the use of cleanroom-approved coatings, antimicrobial and bacteria-resistant coatings, and chemical-resistant floor coatings.
Water and wastewater treatment facilities need painting services that cater to specific operational requirements, like providing resistance to chemicals and protecting surfaces from corrosion and abrasion. Some of the painting services that can be offered to these facilities include coating systems for water storage tanks, containment areas, processing equipment, and floor coatings for treatment areas.
Transportation and distribution facilities require painting services that can safeguard their infrastructure and equipment from wear and degradation. These services often involve the application of exterior paints and coatings that can withstand the elements and provide a professional appearance. Examples of painting services include applying traffic and safety markings for loading docks, hangars, terminals, as well as protecting railings, fences, and exterior walls from weather damage.
Industrial facilities require specialized coatings and paints to protect their structures, machines, and other surfaces that are exposed to harsh conditions such as extreme temperatures, moisture, exposure to chemicals and dust. The primary goal of these coatings and paints is to provide a protective barrier that can extend the life of equipment, reduce maintenance costs, and improve overall operational efficiency. This article will discuss some of the most common types of coatings and paints used in industrial facilities and describe their applications and benefits.
High-performance coatings are designed to provide long-lasting protection for a variety of surfaces in an industrial facility. These coatings are typically more expensive than regular paints but offer many advantages, including improved durability, chemical resistance, and corrosion resistance. High-performance coatings can be used on a wide range of surfaces, from metal to concrete to wood.
One example of a high-performance coating is a fluoropolymer coating, which is designed to provide excellent resistance to chemicals and weathering. This type of coating allows for easy cleaning with minimal maintenance.
Epoxy coatings are a popular choice for industrial applications due to their superior adhesion, chemical resistance, and durability. They are typically used to protect metal surfaces, such as equipment, pipes, and tanks, from corrosion and chemical exposure. Epoxy coatings also have the added benefit of being resistant to water and high temperatures, making them suitable for use in a variety of environments.
Furthermore, epoxy coatings can be applied to concrete surfaces to provide additional protection from heavy foot traffic, chemicals, and abrasion. In some cases, epoxy floor coatings can even be used to dramatically improve the appearance of concrete by adding decorative elements such as colour chips or metallic finishes.
Urethane coatings are known for their exceptional durability and resistance to chemicals, abrasion, and UV rays. They are commonly used on machinery, equipment, and other metal surfaces to protect against corrosion and wear. Urethane coatings also exhibit excellent gloss and color retention, which helps to maintain the aesthetics of the coated surface over time.
Urethane coatings can also be applied to concrete floors, providing additional protection against chemicals, water damage, and impacts. However, it is essential to note that urethane coatings are typically applied over an epoxy primer to ensure proper adhesion to the substrate.
Alkyd or oil-based coatings have been used in industrial settings for many years, primarily for metal surfaces that require corrosion protection. These coatings dry to form a hard, glossy finish that is impact-resistant and can withstand moisture and chemical exposure. However, due to environmental regulations and advancements in coating technology, oil-based coatings are being phased out in favor of more environmentally friendly alternatives.
One of the most significant advantages of oil-based coatings is their ability to penetrate deep into the substrate, providing excellent adhesion and a long-lasting protective barrier. However, the longer drying time and the potential release of volatile organic compounds (VOCs) during application and curing have led to their decreased usage.
Acrylic or water-based coatings are gaining popularity in industrial applications due to their low VOC content, quick drying time, and ease of cleanup. They offer good adhesion, color retention, and resistance to ultraviolet rays, mild chemicals, and abrasion. As a result, acrylic coatings are commonly applied to a variety of substrates, including concrete and metal.
Although acrylic coatings do not offer the same level of chemical and heat resistance as epoxy or urethane coatings, they are still a suitable choice for environments with less exposure to harsh chemicals, such as commercial or residential buildings.
Beyond the general categories, numerous specialty coatings are designed for particular applications or environments within an industrial facility. Some examples include high-temperature coatings, which can withstand extreme temperatures without losing their protective properties; anti-graffiti coatings, which prevent graffiti from adhering to surfaces and enable easy cleaning; and anti-static coatings, which can prevent the buildup of static electricity on surfaces, reducing the risk of explosion or fire in certain environments.
Choosing the right coating or paint for an industrial facility depends on the specific needs and conditions of the environment. Careful consideration should be given to factors such as exposure to chemicals or high temperatures, the level of wear and abrasion, and of course, budget constraints. When selecting an appropriate coating, it is essential to consult with experienced professionals to ensure that the chosen product is applied correctly and will provide the necessary protection and benefits for your facility.
The preparation and application processes for industrial painting projects are essential to ensure the durability, effectiveness, and aesthetic appeal of the final coating. These processes are often guided by industry standards and specifications to achieve a high-quality result. This article will discuss the key steps involved in an industrial painting project, including surface cleaning and preparation, priming, paint application techniques, quality control and inspection, drying and curing, and final inspection and project closure.
Surface cleaning and preparation are critical to the success of any industrial painting project. The goal is to remove all contaminants, such as dirt, grease, and rust, which can impede paint adhesion and result in premature coating failure. There are various techniques for surface cleaning, including power washing, abrasive blasting, and chemical treatments, depending on the nature of the substrate and the type of contaminants present.
Prior to cleaning, all surfaces should be inspected and assessed to determine the appropriate cleaning method. For example, abrasive blasting is a common method used for removing rust and old coatings from metal surfaces, while power washing is suitable for removing loose dirt and debris. Once the appropriate cleaning technique has been selected, all surfaces must be properly cleaned to ensure the primer and subsequent coatings adhere effectively.
Priming is an essential step in industrial painting projects. It helps to create a suitable surface for the subsequent layers of paint to adhere to. A quality primer not only supports the bond between the substrate and the paint, but it also provides additional protection for the surface, reduces the chances of moisture penetration, and can provide a more uniform finish for the topcoat.
There are several types of primers available, such as epoxy, polyurethane, and zinc-rich primers, each with unique characteristics suited to different applications. When selecting a primer, it is essential to consider factors such as substrate material, environmental conditions, and the desired level of protection. Once the appropriate primer has been chosen, it should be applied according to the manufacturer’s instructions to ensure optimal adhesion and performance.
A variety of paint application techniques can be used in industrial painting projects, including brushing, rolling, and spraying. The choice of technique will depend on factors such as the type of coating, substrate, and project requirements.
Brushing and rolling are manual application techniques that use a brush or roller to apply the paint. Brushing is often employed for small or intricate areas, while rolling is typically used for flat or larger surfaces.
Spraying is commonly used for larger scale industrial projects due to its efficiency and ability to provide a uniform, smooth finish. Spray equipment can range from handheld devices to more complex, automated systems. When using spray equipment, proper setup, nozzle selection, and application technique are crucial to achieve a consistent finish.
Throughout the preparation and application processes, quality control and inspections are essential to ensure the successful completion of the project. These inspections typically include checking the cleanliness and preparedness of the surface, verifying the thickness of the applied coatings, and monitoring for defects or issues with the application process.
Various tools and instruments, such as surface profile gauges, adhesion testers, and holiday detectors, can be utilized to assess the quality and integrity of the coating. Regular inspections can help identify issues early in the process, allowing them to be addressed quickly and efficiently, minimizing the risk of costly rework or delays.
After the paint has been applied, it is crucial to allow it to dry and cure properly. Drying refers to the evaporation of solvents from the paint, while curing is a chemical process where the paint hardens and develops its final protective qualities. Both drying and curing are influenced by factors such as temperature, humidity, and air circulation. Following the manufacturer’s guidelines for drying and curing times is essential to ensure the coating achieves optimal performance.
During this process, protective measures must be taken to prevent contamination or damage to the freshly-applied coating. This may include cordoning off the area, restricting access, or even using temporary environmental controls like tents or shelters to regulate the air temperature and humidity.
The final inspection signifies the completion of the industrial painting project. During this inspection, all surfaces should be thoroughly checked for defects, proper coating thickness, and overall appearance. Every aspect of the project should conform to the specified standards and requirements.
Various tools and measurements can be used in this final evaluation, including visual inspection, surface profile measurement, and destructive and non-destructive testing techniques. These assessment methods ensure that the coating has adhered correctly, and quality has been maintained throughout the process.
Upon successful completion of the final inspection, the painting project can be considered closed, and a report should be compiled documenting the work carried out, results of inspections, and any necessary ongoing maintenance or care instructions. Regular maintenance and inspections can significantly extend the life of the coating and maintain its protective qualities over time.
When undertaking a painting project, several environmental and safety factors must be considered to ensure that the job is done properly and with minimal harm to the environment, workers, and the surrounding community. The following sections address several key aspects of this concern, including paint selection, ventilation, handling of hazardous materials, personal protective equipment, and waste management.
The choice of paints and coatings plays a significant role in minimizing the environmental impact of a painting project. It is essential to select paint products that comply with environmental regulations and guidelines. Paint that is low in toxic chemicals, such as volatile organic compounds (VOCs), is a more environmentally-friendly option. The use of low-VOC paint helps to reduce the emission of harmful fumes and to improve air quality. Some eco-friendly paints incorporate natural ingredients or use water-based solvents, which reduces potentially harmful effects on the environment.
When selecting paint, it is essential to purchase the correct amount to avoid waste. Over-purchasing leads to considerable waste, contributing to increased pollution and unnecessary resource consumption. Proper storage and packaging of leftover paint should also be done to avoid leakage and contamination.
Proper ventilation is necessary to preserve air quality and protect workers from harmful fumes during the painting process. Paint fumes can be toxic and may contain VOCs and other harmful airborne particles. Ensuring proper ventilation can minimize the risk of respiratory problems and other health issues resulting from exposure to these fumes.
Various methods can be used to achieve proper ventilation. These include using fans to circulate outside air into and throughout the work area, opening windows and doors, and utilizing air filtration systems designed to remove VOCs and other pollutants. An effective ventilation system helps to maintain a safe environment for occupants and workers and protects the surrounding community from potentially harmful emissions.
The handling of hazardous materials, such as paint thinners, solvents, and other chemicals used in painting projects, must be done with utmost care to avoid environmental contamination and health risks. Safety protocols need to be implemented to ensure proper handling, storage, and disposal of these materials.
Workers should be trained in the proper use, storage, and disposal of hazardous materials. Containers used for storing and transporting these materials must be tightly sealed and labeled according to safety regulations. Secondary containment systems, such as trays or bucket pallets, can be used to catch spills and prevent leaks from contaminating the surrounding environment.
Personal protective equipment (PPE) plays a crucial role in protecting workers from the harmful effects of exposure to paint fumes and chemicals. PPE may include respirators, gloves, safety glasses, coveralls, and other protective clothing. The use of appropriate PPE helps to minimize the risk of injuries and illnesses associated with painting projects.
Workers should receive proper training in the use and maintenance of PPE. They must be educated on the appropriate PPE to use for different tasks, the correct way to wear and remove PPE, and the hazards they may encounter during the project.
Proper waste management and disposal are essential to minimize the environmental impact of painting projects. Waste materials, including used paint, rags, brushes, and containers, must be dealt with responsibly.
Containers, brushes, and other painting tools should be cleaned using a designated area equipped with proper waste collection facilities. Used paint and other hazardous materials should be removed and disposed of according to local regulations, which may entail using designated hazardous waste disposal facilities.
Proper waste management helps to prevent pollution, protect the environment and community, and comply with environmental and safety regulations. By considering the above-mentioned factors, painting projects can be conducted in an environmentally and safety-conscious manner.
In any industrial setting, maintenance and long-term care of the structures and equipment are essential for optimal and efficient performance. Paint and coatings serve a vital purpose in protecting industrial equipment and surfaces against corrosion, wear and tear, and environmental factors. This article will provide information on understanding warranty options, developing a maintenance plan, and implementing regular inspection and repaint strategies to ensure long-term functionality.
Industrial paint and coatings warranties are agreements provided by the manufacturer, guaranteeing their product’s performance within a specified period. The terms of these warranties can vary, so it is essential to understand the limitations and conditions outlined in the manufacturer’s documentation.
There are several factors to consider when reviewing paint and coating warranties:
Coverage: A warranty may cover certain aspects of coating performance, such as resistance to corrosion or damage caused by UV exposure. Be sure to understand which aspects are covered and how long the coverage lasts.
Material and labor costs: Some warranties may cover the cost to repair or replace any failed materials. Some may cover the labor cost to repair the failed materials. Determine which costs are covered by the warranty and whether the expenses are reasonable.
Exclusions: Certain conditions or factors may not be covered under the warranty, such as improper surface preparation or inadequate ventilation. Understand these exclusions to avoid compromised warranty protection.
Claims process: Manufacturers may have specific requirements for filing a warranty claim, such as submitting photographic evidence or allowing an inspector to examine the damage. Familiarize yourself with the claims process to ensure that you can navigate it successfully if needed.
A well-structured maintenance plan is crucial for keeping industrial paint and coatings in good condition. A suitable maintenance plan will not only protect your investment but also ensure the longevity of the painted surfaces. Consider the following when developing a maintenance plan:
Identify areas that need routine maintenance, such as high-traffic zones, exposure to chemicals, or extreme temperature fluctuations.
Establish a schedule for cleaning and inspecting painted surfaces. Regular cleaning helps maintain the paint’s appearance and performance, while routine inspections help identify potential issues before they become significant problems.
Detail the cleaning techniques and products to be used, ensuring they are compatible with the paint and coating materials.
Establish a process for documenting maintenance activities, including any necessary repairs or touch-ups, for future reference and warranty proof.
To ensure the longevity and quality of industrial paint and coatings, implement a regular inspection and maintenance routine. Some best practices include:
Visual inspections: Regularly inspect painted surfaces for signs of wear, such as cracking, peeling, or fading.
Clean surfaces: Remove dirt, dust, and debris from painted surfaces using appropriate cleaning methods (e.g., gentle cleaning with mild soap and water or pressure washing for extreme cases).
Repair damages: Promptly address any paint or coating damages, such as scratches, rust, or abrasions.
Maintain documentation: Record inspection findings, maintenance activities, and warranty information for easy access and reference.
Over time, painted surfaces may require touch-ups or a full repaint to maintain their appearance and protective qualities. Develop a repaint and touch-up strategy to address these needs:
Identify areas where touch-ups are necessary based on inspection findings or through ongoing maintenance records.
Determine the appropriate technique and materials to be used for touch-ups or repainting, ensuring they are compatible with the existing paint and coating system.
Schedule touch-ups and repaints during periods of low production or downtime to minimize disruption to daily operations.
Ensure that any necessary repairs or surface preparation is completed before beginning the touch-up or repaint process.
Industrial painting services cater to various facilities such as warehouses, factories, power plants, storage tanks, bridges, and commercial buildings. The main objective is to safeguard the structures against corrosion, weather, and contaminants while improving their aesthetics.
Surface preparation methods prior to painting include hand/power tool cleaning, abrasive blasting (sand, glass beads, steel shot), high-pressure water cleaning, and chemical cleaning. Proper surface preparation ensures better paint adhesion, resulting in a long-lasting finish.
Electrostatic painting uses a unique technique that creates an electrical charge on the paint particles, making them adhere better to the surface. This allows for more uniform and durable coverage, resulting in reduced material consumption and faster application.
Fireproof coatings are essential in industries where materials or processes pose a high risk of fire. These coatings help protect the structural integrity, prevent fire-related damages, and allow extra time for the safe evacuation of personnel and equipment.
Factors to consider include the type of facility, environmental conditions, substrate material, required durability, and desired appearance. Specific paints are designed to withstand chemical exposure, high temperatures, or provide anti-slip properties to ensure the best results.
Regular paint maintenance, including inspection, cleaning, and touch-ups, ensure that the protective coating maintains its performance. By identifying and addressing any issues quickly, the structure remains secure, minimizing the need for extensive repairs or replacements.
Ready to transform your industrial facility with top-notch painting services? Trust the experts at Alpha Omega Painting. With years of experience and a commitment to excellence, we ensure your facility not only looks its best but also stands the test of time. Don’t wait! Contact us today and let’s bring your vision to life.
Get started with your project today with a quick and easy quote from our friendly staff.
62 Fawcett Road #2, Coquitlam BC, V3K 6V5
Serving Vancouver & surrounding areas with painting & restoration needs.